It’s been a long road to finishing our rerig. Going on 5 weeks now with the mast out, I’ve started to get very antsy to go sailing. Being patient is always the hardest part of any project that takes the boat out of commission (ex, haulouts). After 2 weeks, most projects had been finished and it was just a matter of waiting for BSI to produce the rod.
The downside to rod, as mentioned in Part 1, is it generally can’t be made locally / onsite and therefore takes longer to get. That downside is apparent now in the delays with BSI producing the rod – even though we gave them the end fittings order 5 weeks ago, and final measurements 3 weeks ago, they still haven’t started producing the rigging.
In contrast, a couple weeks ago two new Selden masts arrived in the yard for brand new boats going to the Seattle Boat Show, with wire rigging ready to go, and those masts were fully rigged and stepped in a week.
I wouldn’t change my decision to go to rod – it’s worth it for keeping the mast tang system the same – but if we were buying a new boat someday, I would probably try to avoid rod or would consider it negative points for a boat being considered. It’s a wonderful material, but for a cruiser, availability and ease of access are more important.
Navtec U-Bolt Chainplates
The hardest part of the rerig however (other than the waiting) has definitely been pulling the chainplates for inspection. More specifically, pulling the Navtec U-Bolts above the chainplates.
C&C’s with rod have a somewhat uncommon chainplate system (O’Day’s and Ericsons also have a similar system). At the deck there are six big ½” U-Bolts (one for each shroud) that go through the deck to a thick aluminum backing block. That backing block has a recessed cup on the upper side which is used to capture the head of a stainless steel tie rod. The tie rod then goes down to connect with traditional chainplates inside the boat, attached to a fiberglass bulkhead inside some cabinetry.
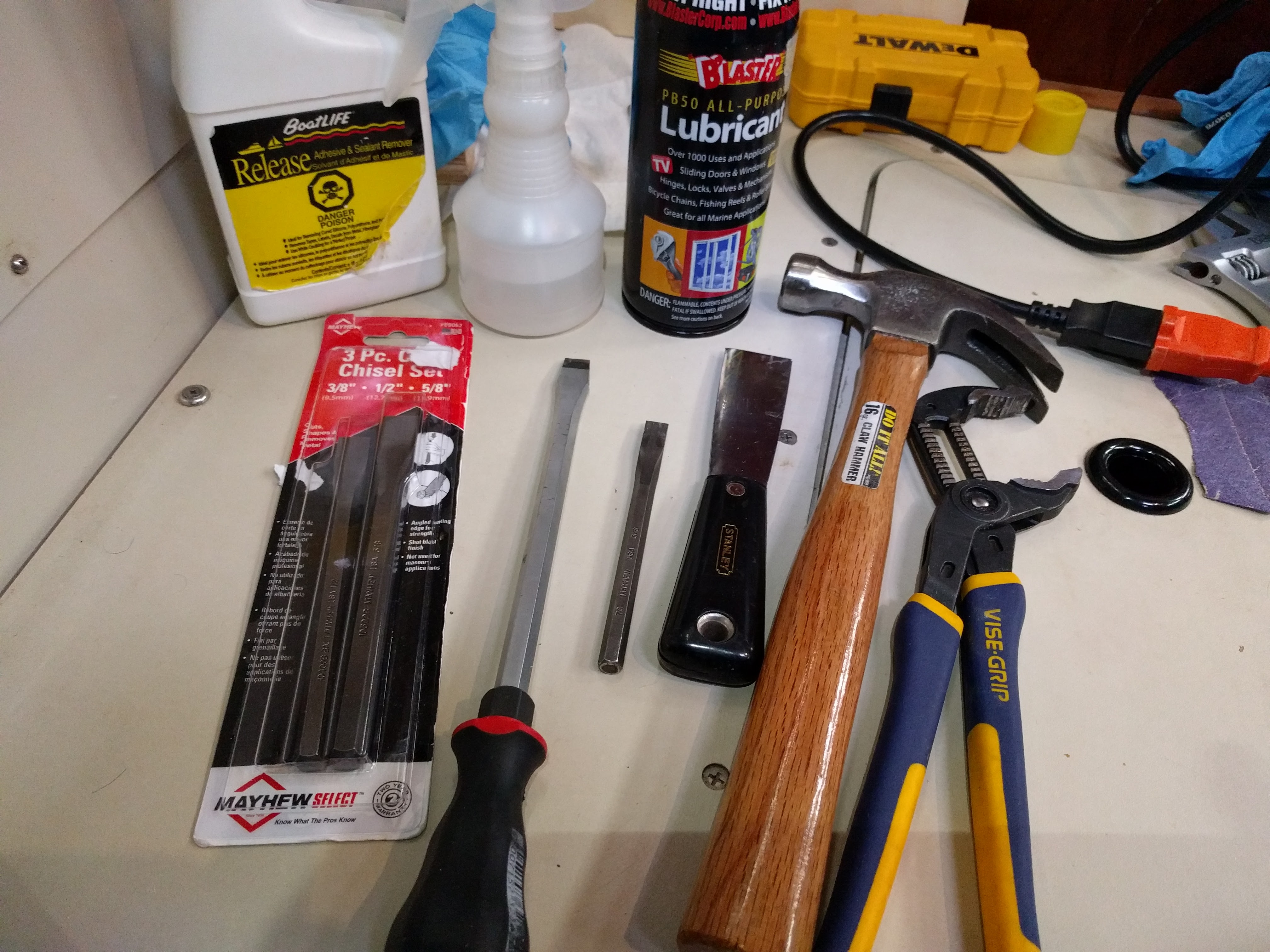
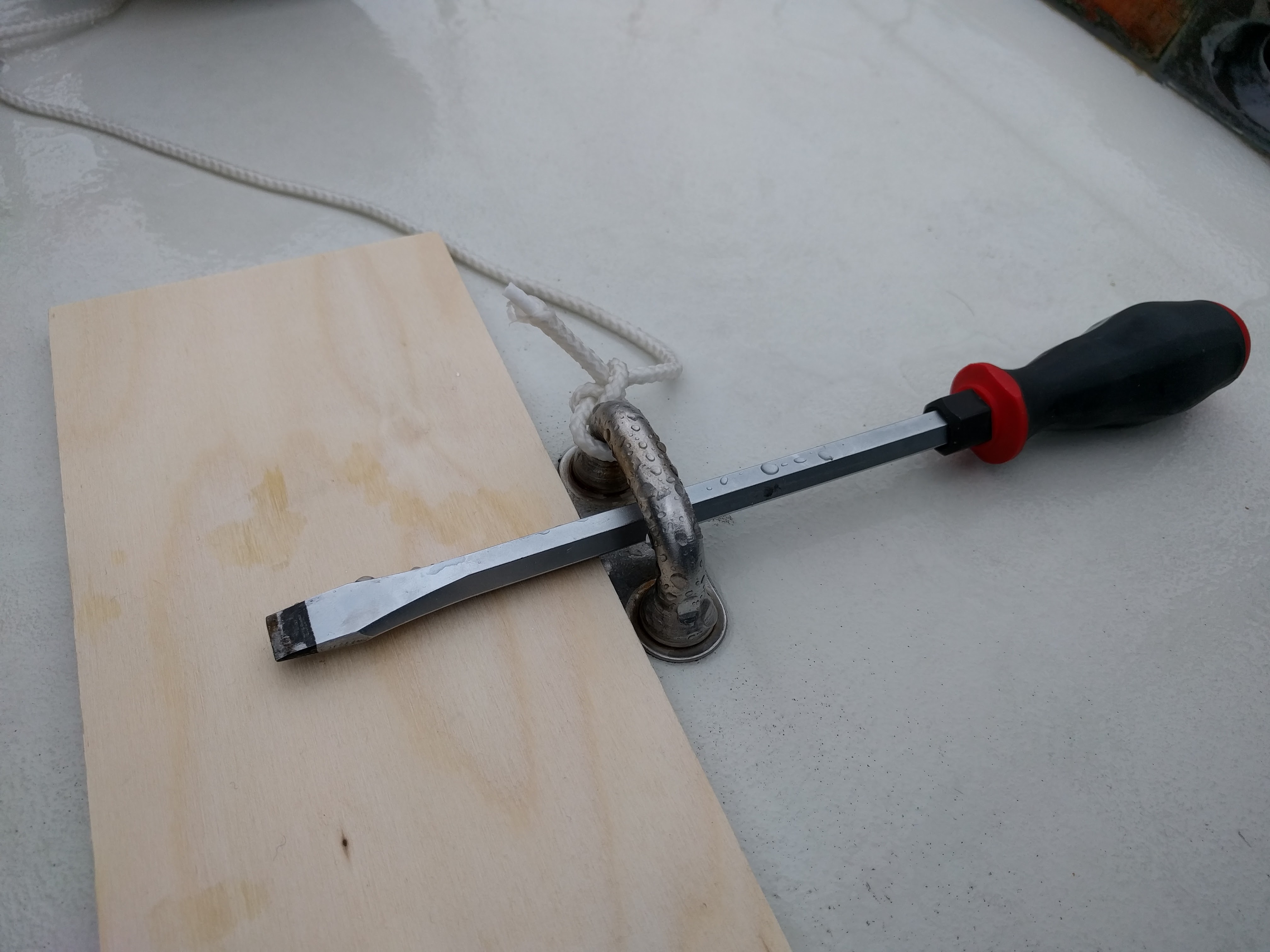
Totally inadequate lever arm for pulling 1/2″ U-Bolts
It’s actually a pretty great design, because the chainplates are completely dry and pristine – I have no concerns about those since they never see water. And the U-Bolts likely do a better job of sealing out water at the deck level than traditional chainplates do. This is because they have a cover plate which fits tightly with the deck, and then the legs of the U-Bolts are flanged (they have a “lip”) so that they are wider than the holes in the cover plate – they overlap it and fit quite snugly.
The downside is they’re really hard to get out. The SS U-Bolt legs interact galvanically with the aluminum backing block, producing pasty white powder which basically locked the U-Bolt into the aluminum block.
Continue reading →