The hardest kind of boat project, in my opinion, is any involving getting stuck things out of the thing they’re stuck in. Seized bolts, corroded screws, prop shaft couplers, etc. You may recall 3 months ago I started the project of rebedding our Navtec U-Bolts that connect the rig to the tie rods and chainplates.
Three months later I had completed 5 out of 6 but still had one stubborn one remaining – the first one I had started on, the last one to finish, and by far the hardest. For whatever reason, the starboard aft U-Bolt was more stuck than all the others. It wouldn’t pull free despite trying all the methods I had used on the others – a 2’ long pry bar, heat, PB Blaster, mineral spirits, BoatLife Release, hammering. I even sailed on it with the nuts slightly loose, and tensioned the shroud to 1500-2000 pounds (this didn’t do anything at all).
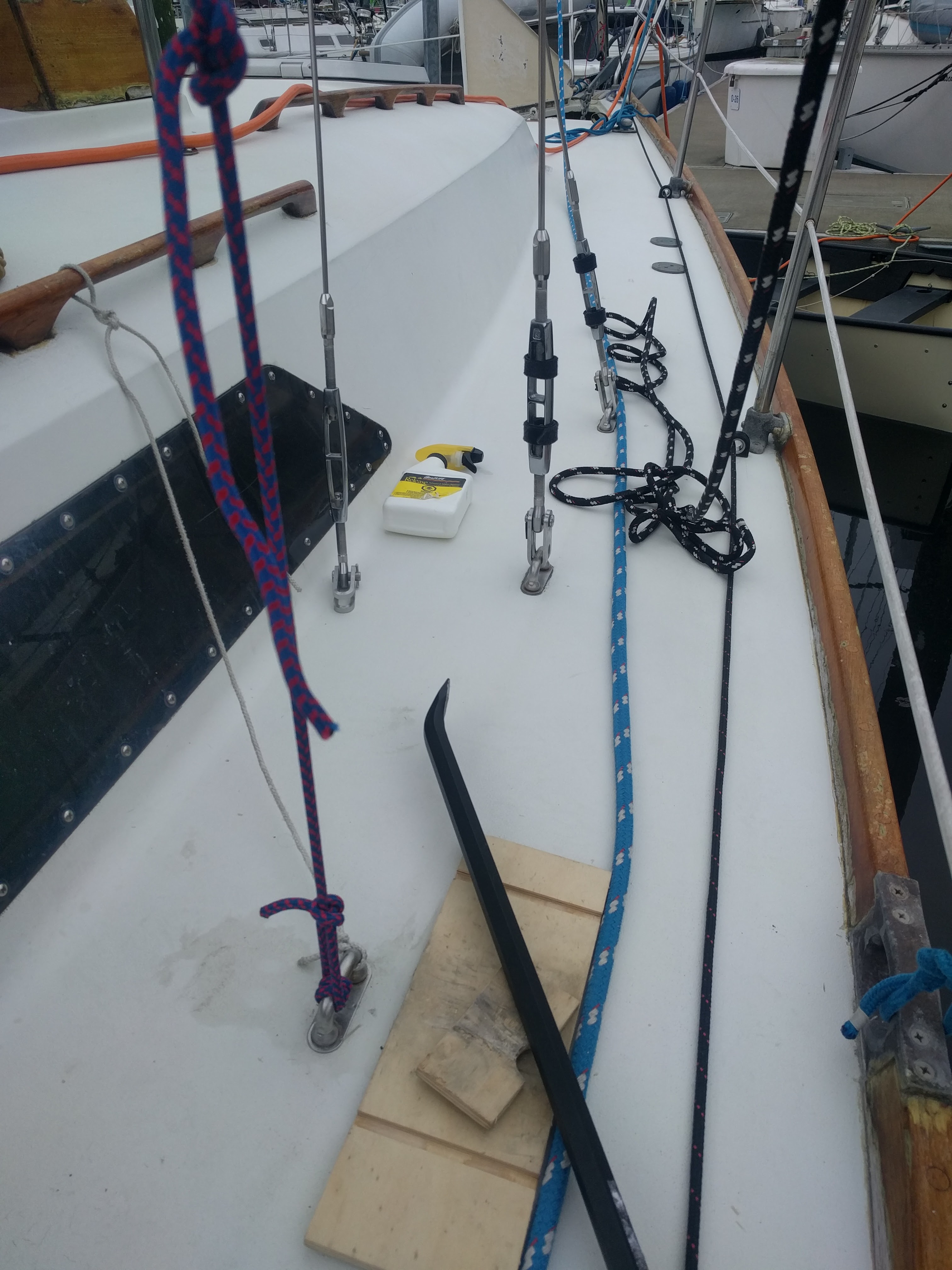
Tensioning the U-Bolt with the main halyard while simultaneously prying with the pry bar
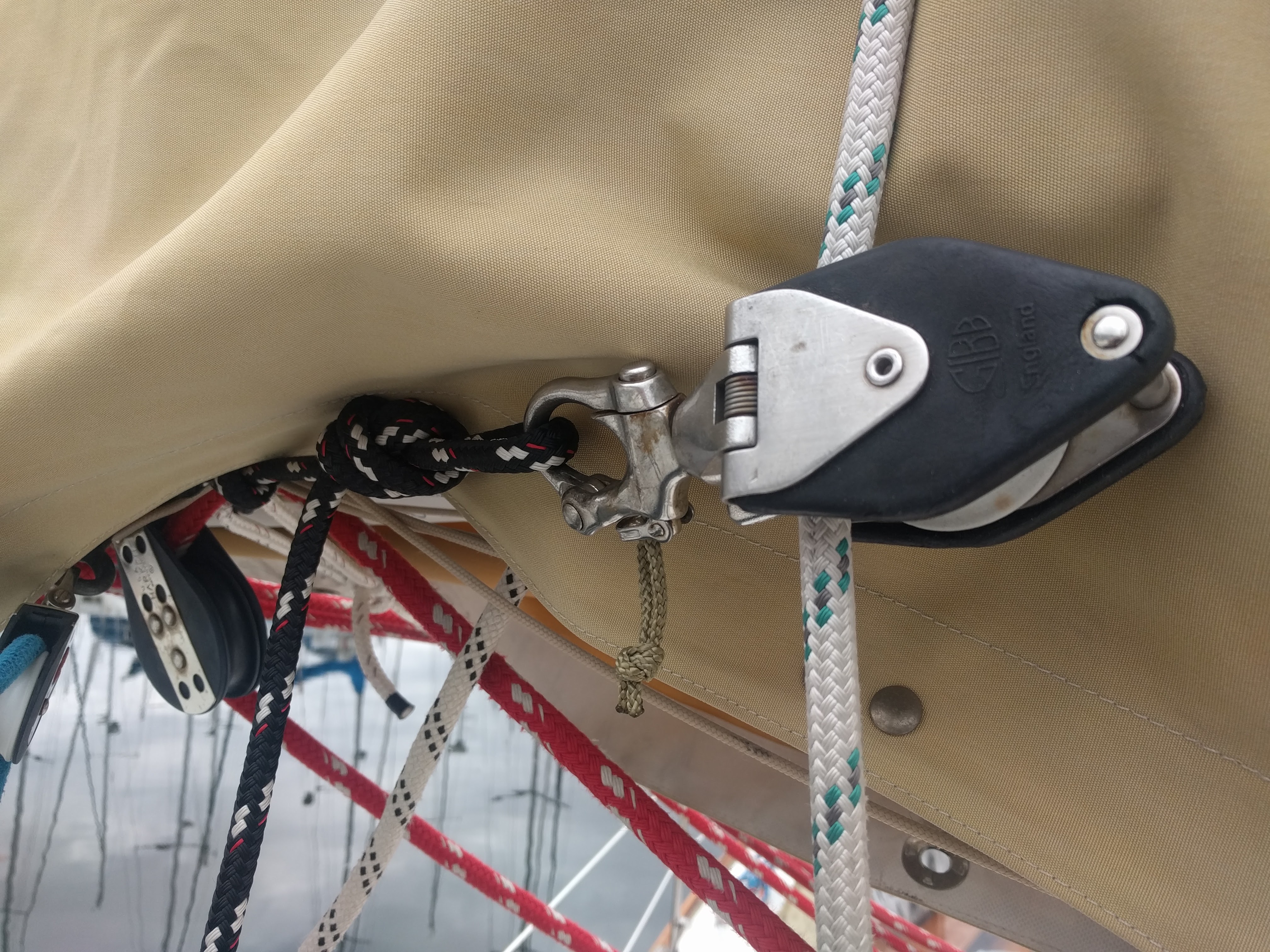
Block on the boom to route the halyard at a good angle.
After another 4 hours of tiring, fruitless prying, heating and hammering, I moved to a new idea – using the main halyard to pull up on the U-Bolt. I was sure this would be the final trick that would work. I rigged up a block on the boom in order to direct the halyard at a proper angle to pull up on the U-bolt. The halyard was tensioned bar tight, as tight as I could get it on the winch – probably at least 2000 lbs of tension. Still, that didn’t help. I leveraged with the 2’ pry bar while the halyard was pulling, and the pry bar helped get one leg of the U-Bolt moving. Progress. But the other leg remained stuck.
Finding the Right Tool for the Job
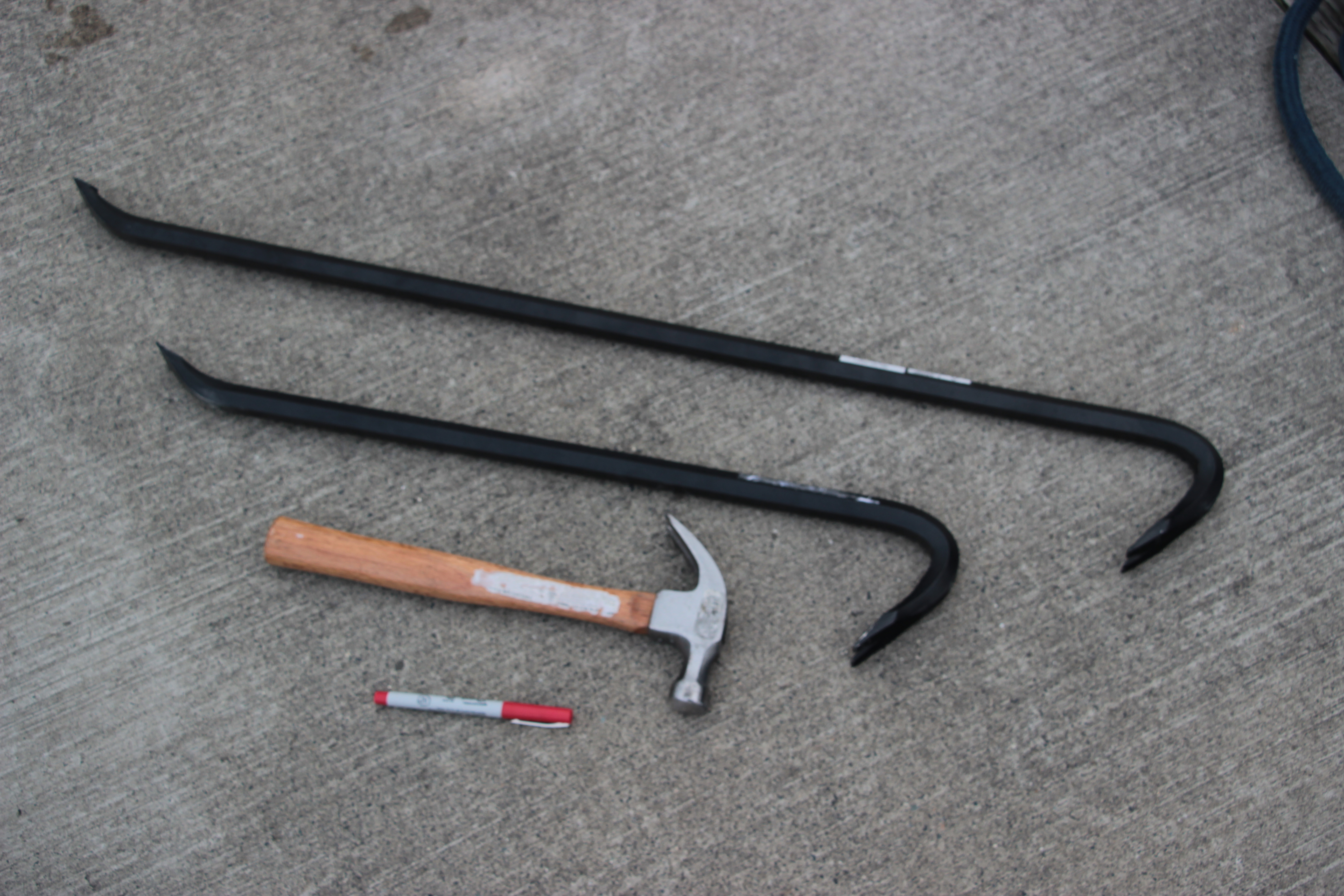
2′ pry bar and 3′ pry bar. The hammer and pen are for context.
With most of these tough something-is-stuck jobs, I find it’s mostly a matter of finding the right tool and techniques.
In this case, the first tool I tried, a 12” screwdriver used as a lever arm / pry bar, was clearly inadequate. The 24” pry bar I got from Tacoma Screw worked for 5 of the 6 U-Bolts but not the last. So, after trying my halyard tension and shroud tension ideas, the next step was a bigger pry bar – a huge three foot long one, again from Tacoma Screw. This is the biggest pry bar they had. I’m finding Tacoma Screw is a great resource for serious tools at very reasonable prices.
And it did the job! It took a few tries and some heat, but I got the remaining leg of the U-Bolt wiggling, and from there it was short work to get the whole thing out.
An important part of the technique is to make sure you’re extracting the U-Bolt legs approximately evenly – ie, if you pull one leg up ½” while the other is fully in the deck, the angle of the bolt will work against getting the remaining leg up. So I used the bolt nuts to pull one leg down while working on the other.
The Gratification of a Project Done Right
It’s probably hard for a reader to understand why I was so happy / relieved to have finished this project. I expect it’s pretty boring to those who have boats that don’t have this kind of U-Bolt. But to me it feels hugely gratifying because it would’ve been so easy to take shortcuts or compromises on this project. I could’ve just ignored the last U-Bolt and it likely would’ve held for many years longer. The aft lower shroud doesn’t take much pressure, and I was applying 2000-3000 lbs on it without any nuts attached to the bolt! 2000-3000 lbs is 20-30% of the rated maximum for this shroud (8000 lbs; the U-Bolts are good to at least 15,000) but in typical sailing it will never see more than 4000 lbs. And it was holding without any nuts on the bolts.
And I considered moving to destructive means like cutting the U-Bolt in half and then twisting to extract it out of the deck. One Ericson owner even drilled a hole into the deck above the backing block and used a drift punch to pound off the backing block, and then repaired the hole with epoxy.
Conclusions
And I think I figured out the question I was perplexed by in the last post – how did the aluminum backing blocks have corrosion when I’ve never seen a leak inside the cabin near them? I think what happens is when the butyl above deck degrades enough to get a small leak, the water just sits on the aluminum backing block. And then once you get enough aluminum corrosion to create the calcified encasement around the U-bolt legs, that acts as a damn and the water probably doesn’t even get past that. So effectively you have below-deck sealing, which is what Maine Sail preaches so much about avoiding.
I suspect this happens on most of these Navtec U-Bolt installations (C&C’s, Ericson’s) but given how few stories there are of people extracting them, I believe most people are just choosing to ignore it. I think they should seriously consider doing the rebedding, because it only gets worse the longer you wait. Like I said, I’ve written way too many posts on the U-Bolts job now, but I’m writing this mainly for future reference – for myself, or anyone else who happens to take on the project.
As a kid I worked a feed mill where the mechanics subscribed to the BFH policy…literally. It was my job to carry a selection of hammers and sledges in ever increasing size, hundreds of feet up the distribution legs so the could bash on recalcitrant parts with just the right amount of force. Never discount using a little more force—the trick is not using too much 🙂
And three months for 6 bolts? You have way more patience than I do. I would have been drilling things out after the first week.
3 months with 1-2 month break in the middle 🙂 Each bolt was about 4 hours, but 1-1.5 of that was cleaning + reinstall, which I don’t mind. The last bolt was at least 12 hours. Came really close to giving up but I didn’t want to pay the desperation tax at RigRite ($300+ for a new bolt). And I wasn’t sure the drill + punch technique would work.